1. Contaminant Removal:
Air preparation equipment is designed to meticulously filter out contaminants that can jeopardize the integrity of a pneumatic system. For instance, a high-quality particulate filter can effectively trap dust and solid particles present in the compressed air. This is crucial in industries where precision is paramount, preventing abrasive particles from causing damage to sensitive pneumatic components such as valves and actuators.
2. Improved Air Quality:
The significance of air preparation equipment lies in its ability to elevate the quality of compressed air. Consider, for example, an automotive manufacturing plant relying on compressed air for precision tools. The removal of impurities ensures that the air delivered to robotic arms and assembly line tools is consistently clean, contributing to precise operations and reducing the need for frequent recalibration.
3. Protection of Pneumatic Components:
In a scenario where compressed air is utilized to actuate pneumatic cylinders in heavy machinery, the absence of air preparation exposes these components to potential damage. Air preparation equipment acts as a shield, preventing contaminants from infiltrating cylinders, valves, and seals. This protective function extends the life of these components, resulting in fewer breakdowns and maintenance interventions.
4. Prevention of Corrosion:
Consider a marine industry application where compressed air is employed in various pneumatic systems. Without proper air preparation, the moisture content in compressed air could lead to corrosion of metal components. Air dryers, integral components of air preparation systems, effectively remove moisture, safeguarding pipes, valves, and other equipment from corrosion and ensuring the longevity of the entire pneumatic infrastructure.
5. Energy Efficiency:
In a manufacturing facility using compressed air for a range of applications, energy efficiency is a critical concern. Air preparation equipment, particularly precision regulators, optimizes air pressure throughout the system. This not only reduces the energy required to operate pneumatic tools but also minimizes waste by ensuring that the air pressure meets the specific demands of each application.
6. Pressure Regulation:
Consider an industrial assembly line where precision is crucial, and different tools require varying air pressures. Pressure regulators in air preparation equipment enable the adjustment of air pressure to meet the specific requirements of each tool. This ensures that each pneumatic device operates at its optimal pressure, preventing damage from excessive pressure and contributing to the overall efficiency of the production process.
7. Lubrication for Pneumatic Tools:
In the case of pneumatic tools utilized in a manufacturing environment, consistent and controlled lubrication is vital for their performance and longevity. Lubricators integrated into air preparation systems deliver a precise amount of lubricant to pneumatic tools at regular intervals. This enhances the tools' efficiency, reduces friction-induced wear, and extends their operational life, ultimately minimizing downtime for maintenance.
8. Enhanced Productivity:
Consider an industrial setting where compressed air powers conveyor systems, robotic arms, and pneumatic drills. The reliability of these systems is directly tied to the cleanliness and stability of the compressed air supply. Air preparation equipment ensures a continuous and reliable flow of clean compressed air, contributing to uninterrupted production processes and, consequently, enhanced overall productivity.
9. Compliance with Industry Standards:
Industries such as pharmaceuticals and electronics manufacturing often operate in environments with stringent cleanliness and quality standards. Air preparation equipment helps these industries meet and exceed regulatory requirements by providing the necessary conditions for clean and regulated compressed air. This adherence to standards is essential for ensuring the quality and safety of the final products.
10. Minimization of System Failures:
In a scenario where compressed air is critical for powering conveyor belts in a packaging facility, the sudden failure of a pneumatic system could lead to production halts. Air preparation equipment significantly reduces the risk of unexpected system failures by maintaining the cleanliness and stability of compressed air. This minimizes downtime, reduces the need for emergency repairs, and enhances the reliability of industrial processes.
Air Preparation-AF1200-30
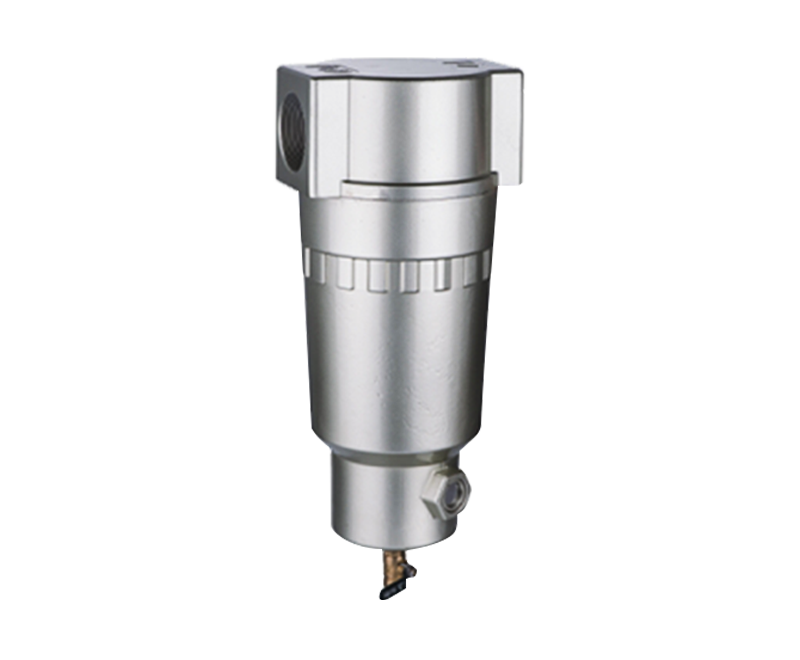
Air Preparation-AF1200-30
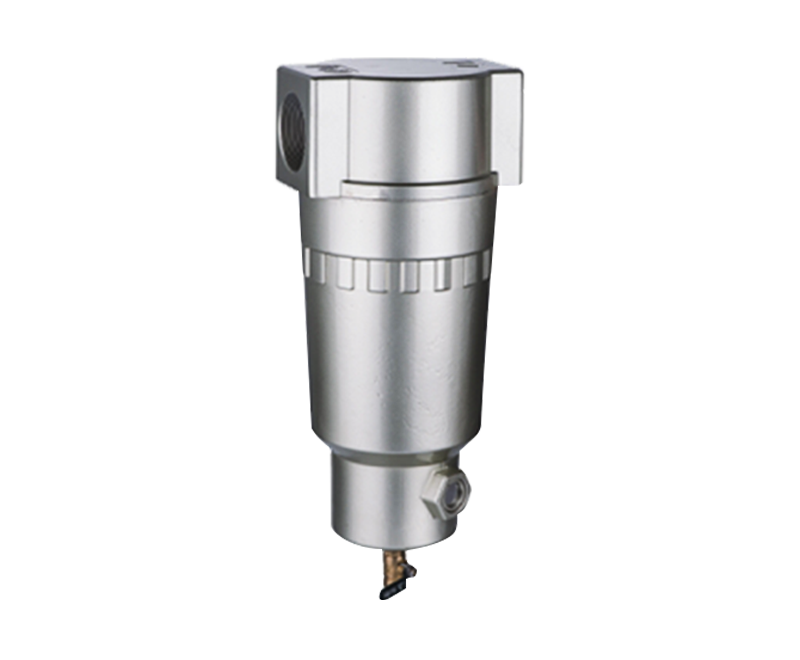